World’s Tallest Prefabricated Skyscraper be built in Singapore by 2023
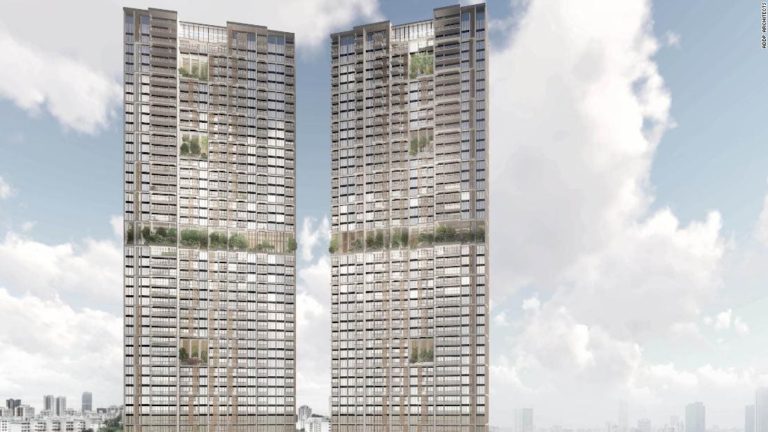
The world’s tallest prefabricated skyscraper is currently under construction and is scheduled to rise in Singapore by 2023, Dubbed the Avenue South Residences, the project will have 988 apartments formed from almost 3,000 vertically-stacked modules done through the building method known as Prefabricated Prefinished Volumetric Construction (PPVC).
The modules are factory-made in Senai, Malaysia, and transported to a Singapore facility to be fitted out and furnished before delivery to the construction site in the residential Bukit Merah district. Named Avenue South Residences, the project comprises of two 192 metre-tall buildings or about 56 floors.
The uniqueness of this project is the Prefabricated Prefinished Volumetric Construction (PPVC) building technic, where the construction is not 100% implemented on the site, but mostly pre-made at a factory in Malaysia. According to the project owner ADDP Architects, after all pieces are installed, the project is about 80% complete. The remaining work is just putting those pieces into position.
The firm also added that PPVC has become popular recently as it can help reduce cost, labour, waste, and noise, especially during the COVID-19 pandemic where social distancing rules are imposed.
Upon completion in 2023, the Avenue South Residences will be the tallest prefabricated skyscraper in the world, surpassing the current 140-metre prefabricated skyscraper in Singapore and two others in London and New York.
According to ADDP Architects, the firm behind the project, the process is similar to the car manufacturing concept. It added that the method is less labor-intensive and can reduce waste and noise pollution. The method limits the amount of construction work carried out at the site to limit noise and allows better-controlled workmanship in factories to reduce waste. The world’s current tallest prefab is the 459-feet Clement Canopy, which is also in Singapore and designed by ADDP Architects.
Singapore’s Building and Construction Authority actively encourages the use of PPVC, citing a 40 percent boost in productivity and an 8 percent savings compared to traditional construction methods.
Large amounts of prefabrication had to be used for the prefabricated skyscraper as the government had determined that PPVC had to be used on the site where the Avenue South Residences will be built.
To raise construction productivity and fundamentally change the design and construction processes, the industry is encouraged to embrace the concept of Design for Manufacturing and Assembly (DfMA), where construction is designed and detailed for a substantial portion of work to be done off-site in a controlled manufacturing environment. The site of Avenue South Residence was selected and set a minimum level of use of PPVC, where this align with government’s initiative to improve construction productivity by up to 40 per cent in terms of manpower and time savings – depending on the complexity of the projects.
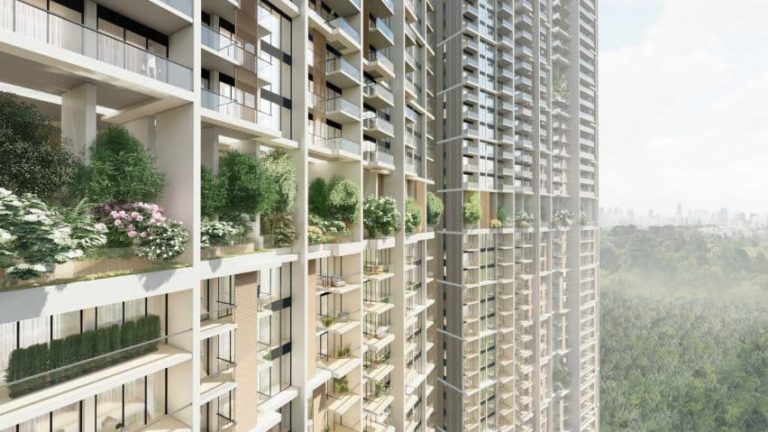
The prefabricated skyscraper style of construction will help reduce the amount of work at the original construction site, creating less waste and noise pollution, minimize disruption for those living nearby, said ADDP Architects. The construction method which first boomed in Europe and America is now significantly spreading its foot in Asia with Singaporean authorities encouraging to use the method as it helps in cost saving among other things.
The prefabricated towers are characterized by simple, sharp lines, and will contain over 1,000 residences broken up by a series of 16 “pocket sky terraces” and larger communal terraces on the 19th and 36th stories. According to the architects, Avenue South Residences prefabricated skyscraper will be in close dialogue with the surrounding area’s nature and green spaces.
Furthermore, the north-south orientation of the high-rises optimizes solar exposure and airflow. They will also be positioned in a way to minimize their footprint, altogether forming a highly energy-efficient development.